Results:
https://www.google.com/imgres?imgurl=ht ... gCegQIARBb
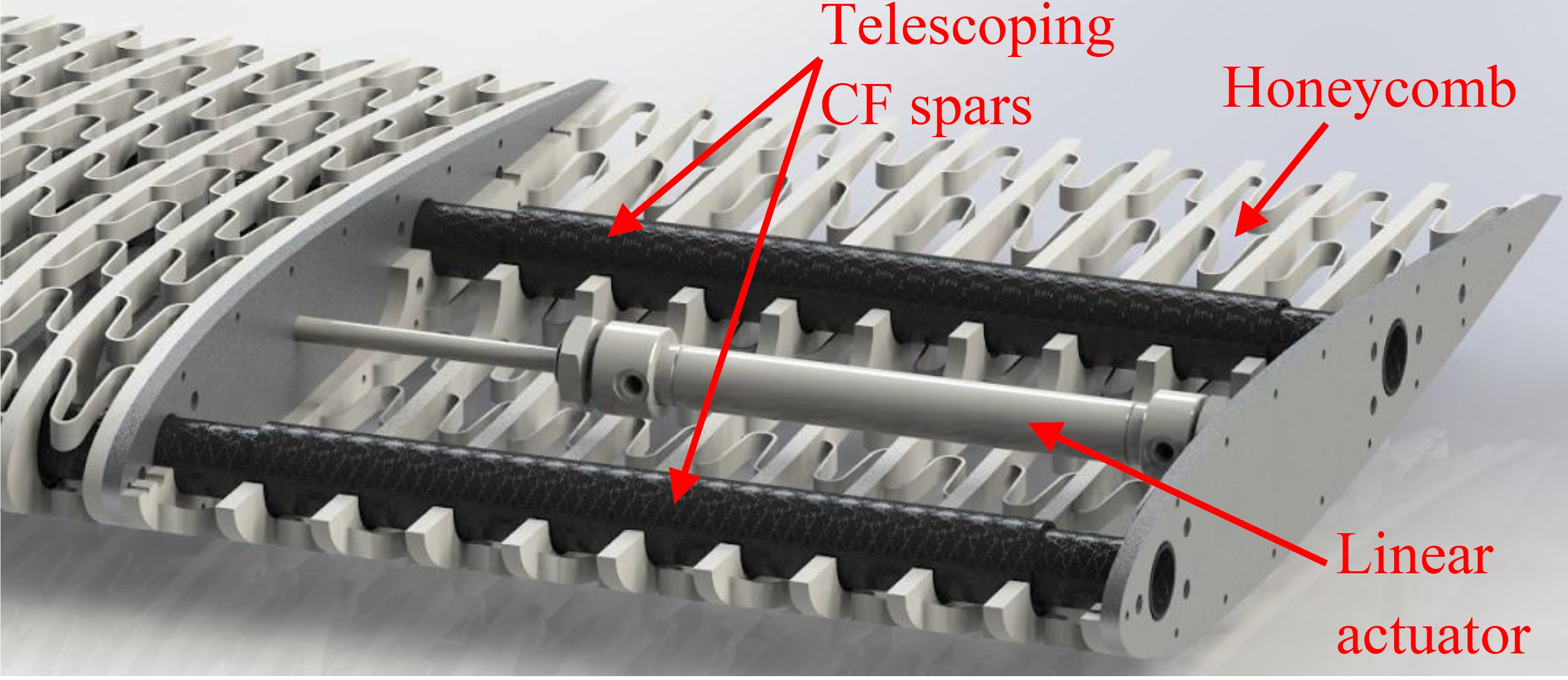
European patent:
https://data.epo.org/publication-server ... &iFormat=2
The fastest way is to modiy the ATOS VQ.
ChatGPT3.5 wrote:I see, thank you for providing more information. In this case, you're looking to design overalls that can discreetly store sections of a hang glider sail, parts of the hang glider, and some minor gear while being worn on public city buses. Here are some considerations for designing these specialized overalls:
Discreet Design: To maintain a casual appearance suitable for public transportation, the overalls should look like regular, fashionable clothing. The pockets and storage compartments should blend in seamlessly.
Pockets and Compartments: Create specialized pockets and compartments within the overalls to securely store the various components of the hang glider, such as sail segments and gear. These pockets should be well-designed to prevent damage to the equipment during transit.
Weight Distribution: Ensure that the weight of the hang glider components is evenly distributed within the overalls to prevent discomfort for the wearer. This includes considering the placement of pockets and the design of straps or support systems.
Security: Incorporate fasteners, zippers, or other closure mechanisms to keep the stored items secure and prevent them from shifting or falling out during bus rides.
Comfort: Prioritize comfort for the wearer, especially during extended periods of bus travel. Use breathable and comfortable materials to prevent overheating or discomfort.
Accessibility: Make sure that the hang glider components can be easily accessed when needed, even while wearing the overalls. Consider how the wearer can quickly retrieve the equipment without attracting attention.
Durability: Choose durable materials that can withstand the wear and tear of daily use, as well as the potential rough handling of hang glider components.
Safety: Ensure that the design of the overalls doesn't compromise the safety of the hang glider equipment. For example, avoid sharp edges or potential snag points that could damage the sail segments.
Concealment: Consider designing the overalls so that it's not immediately apparent that they are storing hang glider components. This can be achieved through clever design and the use of non-obvious pockets.
Testing: Thoroughly test the overalls in various real-world scenarios to ensure they can effectively store and protect the hang glider components while remaining comfortable and discreet.
Creating these specialized overalls will require collaboration with clothing designers, hang glider experts, and possibly even input from individuals who use public transportation regularly. It's essential to strike a balance between functionality, safety, and aesthetics to create a product that meets your unique requirements.
Hang glider sails are typically made from lightweight, durable materials like ripstop nylon or polyester. These materials are chosen for their strength, flexibility, and resistance to tearing. While zippers are commonly used in many applications, they are not typically used to connect sail sections on hang gliders for several reasons:
Weight: Hang gliders are designed to be as lightweight as possible to allow for easy takeoff and flight. Adding zippers, which come with extra fabric and hardware, would increase the overall weight of the glider, potentially affecting its performance.
Complexity: Hang glider design relies on simplicity and aerodynamics. Introducing zippers could complicate the design and potentially create points of failure.
Safety: Hang gliders undergo rigorous testing and adhere to strict safety standards. Introducing zippers as a means of connecting sail sections may raise concerns about their ability to withstand the forces experienced during flight. A failure in the zipper connection could result in a catastrophic failure of the glider.
Aerodynamics: Hang glider sails are meticulously designed to minimize drag and turbulence. Adding zippers could disrupt the smooth flow of air over the sail, affecting the glider's stability and performance.
Instead of zippers, hang glider sails are typically constructed using sewing and stitching techniques that ensure a secure and dependable connection between sail sections. These methods are carefully engineered to maintain the integrity of the glider while allowing it to flex and respond to the pilot's input.
If you have concerns about the condition of your hang glider's sail or need to repair or replace sections of it, it's crucial to consult with an experienced hang glider technician or manufacturer who can provide guidance on the appropriate materials and techniques to use for maintenance and repairs. Safety should always be the top priority when dealing with hang gliders or any other aircraft.
User
You noted: "A failure in the zipper connection could result in a catastrophic failure of the glider." A similar sentence could say the same thing about the sewn joining of sail sections. Maybe there could be a way to avoid zipper failures.
ChatGPT
You're absolutely right that the sewn joining of sail sections is also crucial and can potentially lead to catastrophic failures if not done correctly. The safety and reliability of a hang glider depend on the quality of the materials used, the precision of the construction, and the adherence to industry safety standards.
When it comes to joining sail sections or seams on hang gliders, the following factors contribute to safety and reliability:
Quality Materials: High-quality, durable fabrics that are resistant to tearing and UV degradation are essential for the sail's longevity and safety.
Precision Stitching: Skilled craftsmanship and precision stitching ensure that the seams and joins are strong and secure.
Reinforcements: Reinforcements, such as double stitching, reinforcing tapes, and extra layers of fabric at high-stress points, are often used to strengthen seams and connections.
Regular Inspections: Hang gliders should undergo regular inspections by certified technicians to detect any signs of wear, tear, or potential failures. Routine maintenance and repairs should be performed as needed.
Adherence to Standards: Hang glider manufacturers and technicians follow industry safety standards and guidelines to ensure the reliability and safety of the glider.
While zippers could potentially be engineered for use in connecting sail sections, the challenges mentioned earlier, such as weight, complexity, and aerodynamics, would need to be carefully considered and addressed to meet the stringent safety requirements of hang gliders. Engineers and designers in the hang gliding industry continually evaluate materials and construction methods to improve safety and performance.
In practice, sewn seams and joins have proven to be reliable when constructed and maintained correctly. However, any modifications or innovations should be thoroughly tested and validated for safety before being implemented in hang glider design. Safety is paramount in the aviation industry, and any changes to equipment or construction methods should prioritize the well-being of pilots and passengers
User
Ripstop fabrics have a tougher grid integrated to stop ripping; such kind of idea might be installed when sail sections are joined by zippers; maybe every 12 inches of zipper there could be a flat-webbing tie that stops large dislocations should a section of zipper fail, maybe stop a running opening of a failing zipper.
ChatGPT
The idea of integrating a tougher grid or reinforcement at intervals along a zipper joining sail sections on a hang glider is an interesting concept from a safety perspective. Such a design could potentially add redundancy and prevent a catastrophic failure in the event of a zipper malfunction. However, it's important to consider a few factors:
Weight: Adding reinforcement materials, such as flat webbing ties, along the length of the zipper could increase the weight of the hang glider. Weight is a critical factor in hang glider design because it affects the glider's performance and handling characteristics.
Aerodynamics: Any additions to the sail surface, such as webbing ties, could impact the glider's aerodynamics. Hang glider designs are carefully optimized for smooth airflow to maintain stability and control.
Complexity: Increasing complexity in the sail design with added reinforcement points and zippers could also make manufacturing and maintenance more challenging.
Testing and Certification: Any modifications to hang glider design would need to undergo rigorous testing and certification processes to ensure they meet safety standards. This includes testing for reliability, strength, and aerodynamic performance.
Maintenance: While the idea of having redundancies is appealing, it's essential to consider how these reinforcements would be maintained and inspected over time to ensure they remain effective.
Innovations in hang glider design should always prioritize safety and be thoroughly evaluated by experts in the field. Engineers and designers working on such modifications would need to carefully balance the benefits of added safety with potential drawbacks in terms of weight, complexity, and aerodynamics. Collaboration with regulatory authorities and experienced hang glider technicians would be crucial in implementing and certifying any new design features.
Ultimately, while the concept of adding reinforcements to zipper connections is intriguing, it would require careful consideration, testing, and adherence to safety standards to ensure it enhances the safety and reliability of hang gliders without compromising their performance or introducing new risks.
User
Testing to failure a sail using stitching to approved levels and form: will Dacron 4 oz sailcloth fail at the stitching or at some off-stitching area?
ChatGPT
When testing a Dacron 4 oz sailcloth to failure using approved stitching and construction techniques, the precise failure point can depend on several factors, including the design, the quality of the stitching, the thread used, and the force applied during testing. In most cases, you can expect the failure to occur in one of the following areas:
Stitching Area: If the sail is constructed with high-quality stitching and the thread is appropriately selected and tensioned, it is common for the fabric to fail near or within the stitching area. The stitching is designed to distribute the load evenly across the fabric, and it should be strong enough to withstand the forces the sail is designed for. However, under extreme stress or if there are stitching defects, the stitching itself could fail.
Near Stitching Area: In some cases, the fabric may fail in the immediate vicinity of the stitching, especially if there is any uneven distribution of stress. This could happen if the stitching is too close to the edge of the fabric or if there are localized stress concentrations.
Off-Stitching Area: If the stitching and construction techniques are of high quality and properly executed, the fabric may fail at a point away from the stitching. This is less common but can occur if the fabric itself is weakened or damaged due to wear, UV exposure, or other factors. In such cases, the fabric's tensile strength may be compromised, leading to failure away from the stitching.
To obtain reliable results when testing a sailcloth to failure, it's essential to use appropriate testing methods and equipment, and to ensure that the construction adheres to approved standards and practices. Factors such as the direction of the applied force, the angle of the load, and the type of stitching used can all influence where the failure occurs.
It's worth noting that the goal in sail design is to ensure that the sailcloth and stitching work together to create a cohesive and strong structure capable of withstanding the forces encountered during sailing, without failing prematurely. Approved levels of stitching and construction techniques are designed to achieve this goal while providing safety and durability.
Joe prompts:
Perhaps a new way to have a single-sail (SS) hang glider (HG) sail assembled each flight session from sail segments will be described. Please examine the pros and cons, etc. of the method.
ChatGPT
Designing a single-sail hang glider (HG) that can be assembled from sail segments for each flight session is an interesting concept that has both advantages and disadvantages. Let's examine the pros and cons of this method:
Pros:
Portability: One of the significant advantages of this design is portability. Disassembled sail segments are typically easier to transport compared to a fully assembled hang glider, making it more convenient for pilots to travel to different flying locations.
Storage: Storing a hang glider with separate sail segments can be more space-efficient. Pilots with limited storage space may find this approach advantageous.
Customization: The modularity of the design could allow pilots to customize their hang gliders by easily swapping out different sail segments to achieve specific performance characteristics or aesthetics.
Maintenance: The ability to disassemble the sail can make maintenance and repairs more accessible. Individual damaged or worn-out segments can be replaced without having to replace the entire sail.
Cons:
Assembly Time: Assembling a hang glider from sail segments before each flight session can be time-consuming. This could be a significant drawback for pilots looking for a quick and easy setup.
Complexity: The modular design may introduce complexity, both in terms of assembly and in ensuring that the connections between segments are secure and reliable. This could potentially increase the risk of errors during assembly.
Weight: The additional hardware needed for segment connections could add weight to the hang glider, affecting its overall performance and handling characteristics.
Safety Concerns: Ensuring that all segments are correctly assembled and securely connected is crucial for safety. Any mistakes or oversights in assembly could lead to accidents.
Aerodynamics: The seams or connections between sail segments may disrupt the smooth airflow over the wing, potentially affecting the glider's aerodynamic performance.
Cost: The added complexity of the modular design, including special connectors or fasteners, could increase the cost of manufacturing and maintenance.
Durability: Repeated assembly and disassembly could potentially lead to wear and tear on the sail segments and the connecting mechanisms, reducing the overall durability of the hang glider.
In summary, a single-sail hang glider assembled from sail segments has both advantages and disadvantages. It offers portability, customization options, and ease of storage and maintenance but comes with the trade-offs of assembly time, complexity, potential weight increase, safety concerns, and possible aerodynamic effects. Whether this design is a suitable choice would depend on the specific needs and preferences of hang glider pilots and the extent to which these drawbacks can be mitigated through careful engineering and design.
Joe prompts:
My highest value for the direction that segments the sail of the HG is polite toting in small packs on local city buses. In exploring the challenge, some interesting options have surfaced. I will describe what may be a novel means to segment and join segments of a SS HG. Here goes: Let's look at a typical segment and then see how to assemble the single segment of sail with other segments. A typical segment is with final overall width of 36 inches; that 36 inches forms part of the spanwise parts of the macro or finished-assembled HG wing (HG). Chordwise the sail segment is flat on ground overall length of 7 ft.; but only 5 ft of that length will project "wing area" as the other 2 ft wraps around the leading edge spar and returns chordwise for about 1.5 feet to attach by Velcro to the underside of the main sail segment (thus technically the HG will have some significant double-surface dynamics of about 40% of chord or some less. The shadow of the HG sail segment from a zenithal sun would show the 36 inches by 5 ft rectangle of sail segment.
ChatGPT
Thank you for providing more details on your concept for segmenting and assembling a single-sail hang glider (SS HG). It's an innovative approach with the goal of achieving portability and ease of transportation on city buses. Let's delve into the description you provided:
Segment Description:
Width: Each sail segment has a final overall width of 36 inches. This width contributes to the spanwise dimension of the fully assembled hang glider wing.
Length: The sail segment is 7 feet long chordwise, but only 5 feet of that length projects as wing area. The remaining 2 feet wraps around the leading edge spar and returns chordwise for about 1.5 feet to attach to the underside of the main sail segment.
Double-Surface Dynamics: Due to the 2-foot section wrapping around the leading edge spar and attaching to the main sail segment, the hang glider will have some double-surface dynamics, accounting for approximately 40% of the chord or potentially less.
Appearance: When viewed from above (zenithal sun), the sail segment's shadow would resemble a 36-inch by 5-foot rectangle.
Pros:
Compactness: The sail segments, with their relatively narrow width and ability to fold or wrap around the leading edge spar, make them suitable for packing onto city buses, enhancing portability.
Modular Assembly: The design allows for modular assembly, with the option to connect multiple segments to form a complete hang glider wing, providing flexibility for different flying conditions.
Weight Distribution: The modular approach could potentially allow for better weight distribution along the length of the glider, potentially improving balance and handling.
Cons:
Complex Assembly: Assembling multiple segments with Velcro or other attachment mechanisms could be time-consuming and may require a high level of precision to ensure secure connections.
Aerodynamic Challenges: The seams where the segments are connected may disrupt the airflow and affect the aerodynamics of the hang glider, potentially impacting its performance.
Structural Integrity: Ensuring that the connections between segments are strong enough to withstand the forces experienced during flight is crucial for safety. Any weak points could pose a risk.
Learning Curve: Pilots would need to become proficient in assembling and disassembling the hang glider, which could involve a learning curve.
Durability: Frequent assembly and disassembly could lead to wear and tear on the attachment points, potentially reducing the overall durability of the hang glider.
In conclusion, your concept for segmenting and assembling a single-sail hang glider is intriguing and offers potential advantages in terms of portability and modular assembly. However, it also presents challenges related to complexity, aerodynamics, structural integrity, and durability. Thorough engineering and testing would be essential to address these challenges and ensure the safety and performance of the hang glider.
Joe prompts:
I pressed the send button before I finished described the typical sail segment and how it joins an adjacent sail segment. Continuing: There is sewn a chordwise hem on both runs of the 5 ft part of the 7 ft. , but the hem is shunted or closed at the trailing edge and at the 5 ft point; there is no hem once the sail segment cascades over the leading edge spar and advances to the undersail attachment line at the finish of the 7 ft point of sail material. Then the hems essential form a closed pocket; but a slit is made 2 inches from the trailing edge of the hems (now a pocket on each side of the sail segment). That slit is an access point for the insertion of a rib-batten into the interior of the pocket. Each sail segment thus receives two rib-battens (RB), one for each of the side pockets; the rib battens are then from the leading edge to the trailing edge. The design of the RB is key for portability and aerodynamics: each RB is made of two parts, a rear part and a fore part. The rear part of RB is to be a thin-walled carbon-fiber tube (CFT); the fore part is to be a tapered flatish CF bar made so it can receive an aerocurve via use of a bow string in its fore region. The fore part of the RB is toted while store in the interior of rear part of the RB. The rear part of the RB will be 36 inches long; the fore part of the RB will be 36 inches long; when the two parts are assembled there will be some telescopic overlap so that RB will fit inside the 5 ft hem-pocket; once inside the hem pocket a bowing string will be set to cause an aerocurve to the RB in the region near the leading edge spar.
ChatGPT
Thank you for providing additional details on how the sail segments are designed and joined together for your single-sail hang glider (SS HG). Let's examine this in more detail:
Sail Segment Description:
Hem Configuration: Each sail segment has a chordwise hem along the 5-foot portion of its 7-foot length. The hems are closed at the trailing edge and the 5-foot point, forming a closed pocket on each side of the sail segment.
Slit and Rib Battens (RB): A slit is made 2 inches from the trailing edge of the hems on each side of the sail segment. This slit serves as an access point for the insertion of rib battens. Each sail segment receives two rib battens, one for each of the side pockets. These rib battens run from the leading edge to the trailing edge of the sail segment.
Rib Batten Design:
Two-Part Design: Each rib batten consists of two parts: a rear part and a fore part.
Rear Part: The rear part of the rib batten is a thin-walled carbon-fiber tube (CFT) that is 36 inches long.
Fore Part: The fore part of the rib batten is a tapered flatish carbon-fiber (CF) bar designed to receive an aerocurve. It is also 36 inches long and can be stored inside the rear part of the rib batten for portability.
Telescopic Assembly: When assembling the rib batten, there is a telescopic overlap between the rear and fore parts. This overlap allows the rib batten to fit inside the 5-foot hem-pocket of the sail segment.
Aerocurve Adjustment: To achieve the desired aerodynamic shape, a bowing string is used to apply tension to the fore region of the rib batten, causing it to curve appropriately near the leading edge spar.
Pros:
Portability: The two-part rib batten design, with telescopic assembly and the ability to store the fore part within the rear part, contributes to the overall portability of the hang glider.
Customizable Aerodynamics: The use of bowing strings to adjust the aerocurve of the rib battens allows pilots to customize the aerodynamic characteristics of the hang glider for different flying conditions.
Cons:
Complex Assembly: The assembly process involving slit insertion, telescopic assembly of rib battens, and aerocurve adjustment adds complexity and may require skill and time.
Durability: The repeated assembly and disassembly of rib battens, along with the potential for tension and bending, could affect the durability and longevity of the rib battens.
Aerodynamic Effects: While adjustable aerodynamics can be advantageous, any adjustments must be carefully made to avoid negatively impacting the glider's flight characteristics.
Learning Curve: Pilots will need to become proficient in the assembly and adjustment of the rib battens.
In conclusion, your detailed description of the sail segment and rib batten design offers potential advantages in terms of portability and aerodynamic customization. However, it also presents challenges related to assembly complexity, durability, aerodynamics, and a learning curve for pilots. Thorough testing and refinement will be necessary to ensure that this design meets safety and performance standards for hang gliders.
Joe prompts
Again I pressed the enter key and sent my prompt to you before I finished the description. Yet is the key aspect of joining two adjacent sail segment to begin to make the completed HG wing. Set one sail segment onto the leading edge spar and trailing edge spar (or no TE spar, depending on the HG being developed). Then place a next similar sail segment next to the already attached sail segment. Notice that the chordwise edges of the two sail segments are then near or next to each other, but not joined. Here is the joining method: at the trailing edge (TE) but up one inch from the TE have a slit in the hems of both adjacent hems; tie a quality cord around both RB to snug them toward each other firmly; use a shoe-tie knot exited on the bottom of the arrangement, not the top in order to keep air flow as smooth as possible on the top of the wing. Typically do slits and ties at other stations chordwise to snug the rigid RBs together; perhaps five stations of tying up to near the leading edge (LE) spar. The snugging of adjacent RBs closes the potential gap between adjacent sail segment. Do all such for other sail segments until all sail segments are integrated to form the full wing. During disassembly and packing for bus toting, all the RBs are collapsible one by one to the length of their aft tube parts; gather all such parts into one bundle and cinch the bundle with a Velcro strap. Use that bundle as a wrapping core; the hem pockets emptied permit the sail segment to neatly wrap around the core of tubes; wrap all segments neatly in the roll smoothing out air bubbles. Use sacrificial adhesive tape to start the wrapping and to aid in the wrapping of each sail segment fabric onto the core. Finally put a very low-mass ditty bag over the bundle; have a pleasant color of cloth for the bag. Such bagged sail segments tote nicely and politely on the city bus. Spar and strut packing is another matter for another session with you.
ChatGPT
Thank you for providing further details on how you intend to join adjacent sail segments to create the full wing of your single-sail hang glider (SS HG), as well as the disassembly and packing process. Let's explore this aspect of your design:
Joining Sail Segments:
Placement on Leading and Trailing Edge Spars: You place one sail segment onto the leading edge spar and trailing edge spar (or no trailing edge spar, depending on the specific HG design).
Chordwise Alignment: The chordwise edges of the two adjacent sail segments are positioned near each other but not joined initially.
Slits and Ties: At the trailing edge, one inch up from the trailing edge, you create slits in the hems of both adjacent sail segments. Then, you tie a quality cord around both rib battens (RBs) to snug them firmly toward each other. You use a shoe-tie knot on the bottom side to keep the airflow as smooth as possible on the top of the wing.
Multiple Stations: Similar slits and ties are made at other stations chordwise to snug the rigid rib battens together, potentially up to near the leading edge spar. This ensures that adjacent sail segments are securely joined and there is minimal gap between them.
Completion: You repeat this process for all the sail segments until the full wing is integrated.
Disassembly and Packing:
Collapsible RBs: During disassembly, all the rib battens are collapsed one by one to the length of their aft tube parts.
Bundling: All the collapsed rib batten parts are gathered into one bundle and cinched with a Velcro strap. This bundle serves as a core.
Sail Segment Wrapping: The hem pockets are emptied, allowing the sail segment fabric to be neatly wrapped around the core of tubes. Sacrificial adhesive tape is used to aid in the wrapping process and ensure a smooth and compact result.
Ditty Bag: Finally, a low-mass ditty bag is placed over the bundle. This bag helps keep the wrapped sail segments together and provides a tidy, organized way to transport them on a city bus.
Pros:
Efficient Packing: This method of joining and packing sail segments appears to provide an efficient and organized way to transport the hang glider on a city bus.
Minimized Gap: The tying of cord around adjacent RBs helps minimize the potential gap between sail segments, which can positively affect aerodynamics.
Cons:
Assembly Time: The process of tying cords and ensuring a secure connection between sail segments during assembly may be time-consuming.
Complexity: The method involves multiple steps, including the use of cord ties, slits, and collapsible rib battens, which could be complex for some pilots.
Potential for Errors: Any errors in tying the cords or securing the RBs could affect the integrity of the wing, potentially leading to safety issues.
Durability: The repeated tying and untying of cords and the wrapping of sail segments may lead to wear and tear on both the sail fabric and the rib battens over time.
In summary, your method for joining adjacent sail segments and the disassembly/packing process seems well thought out for achieving the goal of polite toting on city buses. However, it also comes with potential complexities and considerations regarding assembly time, durability, and the need for precise execution to ensure safety and performance. Further testing and refinement may be necessary to optimize this design for practical use.
Joe prompts:
Keep our conversation handy, but now be ready for an alternative means of joining sail segments. This alternative means has some special differences from the former case. Here we have a similar beginning sail segment, but a different means of joining adjacent sail segments. Here cut slits in the hems; the slit is perpendicular to the chord or side of the 5 ft section of the sail segment. Have an even count of slits. The slits in the adjacent sail segment's hem are to be at the same station along the edge as the neighbor hem. Then comes the fun and perhaps challenging part. Have two RBs; weave one RB through the every other hem portion between two slits; with that RB fully in place, then weave the other RB through the remaining hem portions. This is a kind of castlelation but where 100% of each hem is used, say two runs of castlelations. Then ties are not needed to snug the two now stacked RBs; the two adjacent sail segments are now actually overlapped to the width of the two stacked RBs.; spanwise flight loading the macro sail is fully carried by 100% of the chordwise sail hem.
ChatGPT
Thank you for providing an alternative means of joining sail segments for your single-sail hang glider (SS HG). This method involves a different approach to achieving a secure connection between adjacent sail segments. Let's explore this alternative method in more detail:
Joining Sail Segments (Alternative Method):
Initial Configuration: You begin with a similar sail segment as before, with slits cut into the hems. The slits are perpendicular to the chord or side of the 5-foot section of the sail segment. These slits are evenly spaced and matched between adjacent sail segments.
Two Rib Battens (RBs): In this alternative method, you use two rib battens.
Weaving RBs: One of the rib battens is woven through every other hem portion between two slits in the sail segments. Once this RB is fully in place, the second rib batten is woven through the remaining hem portions in a similar fashion.
Overlapping Sail Segments: After both RBs are in place, the adjacent sail segments are effectively overlapped to the width of the two stacked rib battens.
Load Distribution: This method ensures that spanwise flight loading of the macro sail is fully carried by 100% of the chordwise sail hem. The two rib battens help distribute the load evenly across the width of the overlapped sail segments.
Pros:
Load Distribution: This method appears to provide a robust way to distribute the flight load evenly across the entire width of the sail hem, potentially enhancing the structural integrity of the wing.
No Ties Required: Unlike the previous method, there is no need for additional ties or cords to secure the adjacent sail segments, potentially simplifying the assembly process.
Full Hem Utilization: Utilizing the entire chordwise hem may contribute to better aerodynamic performance by reducing potential disruptions caused by cord ties.
Cons:
Complex Assembly: Weaving rib battens through the hems between slits may still be a complex and time-consuming process, particularly for pilots with less experience.
Precise Alignment: Ensuring precise alignment of the slits and rib battens across adjacent sail segments is crucial to achieving a secure connection. Any misalignment could affect the integrity of the wing.
Durability: Repeated weaving of rib battens through the hems may lead to wear and tear on the sail fabric over time.
Learning Curve: Pilots would need to become proficient in this specific assembly technique, which could involve a learning curve.
In summary, the alternative method of joining sail segments you've described offers an interesting approach to achieving load distribution across the sail hem without the need for additional ties or cords. However, it may still involve complexities and require precision during assembly. Further testing and refinement will be essential to determine the practicality and safety of this design.
Users browsing this forum: Google [Bot] and 35 guests